<div class=”warehousingchallengespart2aeo”>
<p><strong>What are the biggest warehousing challenges in 2024?</strong><br>
This blog explores the top 5 supply chain and warehousing issues facing logistics leaders today — from talent shortages and inventory visibility gaps to automation fatigue and data fragmentation. Part 2 of our countdown series dives into real-world problems and integration-driven solutions used by top-performing 3PLs, retailers, and manufacturers.</p>
</div>
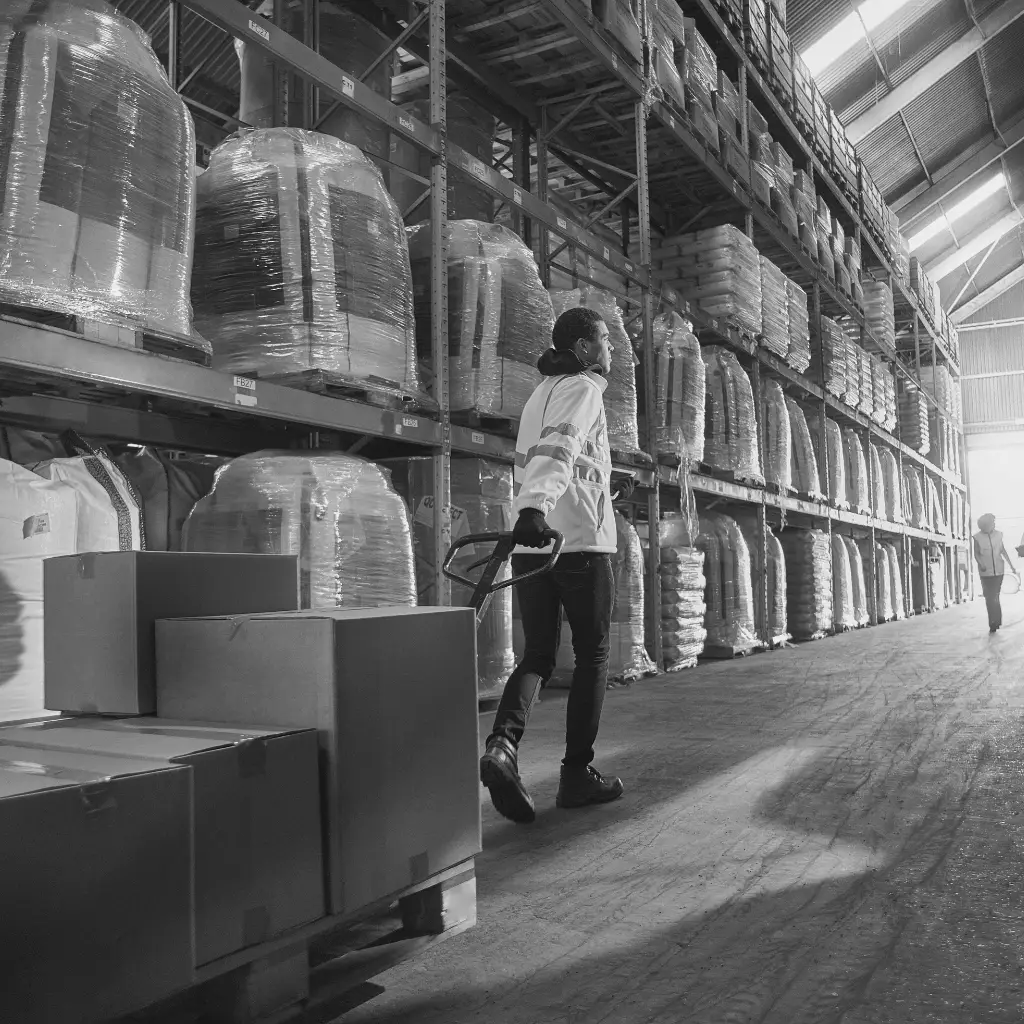
Inaccruate inventory data is one of the most glaring issues a warehouse can have.
To continue our discussion on warehouse challenges, we will explore five more critical areas that often require attention in most warehouses. From enhancing staff training to optimizing space utilization, these issues can significantly impact overall warehouse performance. Let’s delve into these additional areas to better understand how to overcome them.
5. Flawed Order Fulfillment/Picking Process
Order picking is one of the most critical tasks in a warehouse. If orders are not fulfilled accurately and promptly, consumers may have a poor experience, leading to negative outcomes such as them not returning, leaving bad reviews, or sharing their dissatisfaction with others. These consequences can result in decreased sales opportunities.
Research indicates that 50-70% of a picker’s time is spent moving around the warehouse rather than actually picking items. Addressing this inefficiency is crucial to ensure that order fulfillment is both efficient and straightforward. The physical warehouse setup, as discussed earlier, significantly impacts this process. Additionally, employing different picking strategies, such as batch picking, wave picking, and discrete picking, can streamline the task for team members. Each strategy has its pros and cons, which should be carefully considered before implementation.
4. Difficulty Adapting to Fluctuations in Demand
Consumer demand fluctuates for various reasons, some predictable, like holiday seasons, and others unpredictable, such as changes in consumer tastes or economic downturns. While these shifts are beyond control, the warehouse’s response to them can be managed. Avoiding inventory gaps and ensuring seamless fulfillment during demand surges are crucial for managing the challenges of seasonal fluctuations.
Leveraging technology like predictive analytics and understanding customer buying behavior can provide a significant advantage. Guiding consumers through targeted marketing and advertising campaigns can help direct purchases towards available stock, mitigating the impact of out-of-stock items.
Maintaining strong relationships with vendors, and having backup suppliers for instances when demand exceeds normal capacity, is also essential. Flexibility and contingency planning are key to handling unexpected situations.
3. Mismanaged Labor
Labor can account for 55-65% of total warehouse operation costs (excluding shipping). Effective staff management is crucial for improving overall productivity and accuracy in shipping and receiving processes. Mismanagement can lead to high turnover, inefficiencies, poor work culture, and safety issues.
Hiring and training the best staff can help avoid these problems. It’s also important to ensure the warehouse is adequately staffed based on shipment volumes. During seasonal peaks, such as holidays or local produce seasons, understaffing can lead to safety issues and increased turnover.
Investing in training and development, offering competitive compensation, and prioritizing workplace safety are critical. Happy, well-rested staff are vital to the business’s bottom line.
2. Inefficient Use of Space
Poorly configured warehouses contribute to many of the challenges on this list, particularly poor inventory management. The average warehouse utilizes only about 68% of its usable space, meaning that 32% of space is being paid for but not used effectively. For example, if you’re paying $200,000 a month for warehouse space, approximately $64,000 is being wasted.
Additionally, errors in warehouse setup can lead to inefficient picking of high-volume items if they are not properly placed.
There are companies and technologies available to assist with proper warehouse configuration, collaborating with teams to ensure efficient flow of people and products within the warehouse. Solutions to consider include vertical storage systems, optimizing aisle widths, and slotting optimization (placing high-volume items in easily accessible locations).
1. Inaccurate Inventory Data
Inventory data issues are among the most noticeable and well-known challenges in the warehouse industry. The problem isn’t just in identifying the issue but in dealing with it efficiently and cost-effectively. Inventory data inaccuracies can lead to ineffective picking, incorrect reordering, and consumer dissatisfaction when items listed as available are actually out of stock. Many companies still rely on manual processes to update inventory data, inevitably leading to errors.
Addressing inventory data issues can be daunting and costly, but the longer it’s delayed, the more expensive and complex the solution will become. Implementing a Warehouse Management System (WMS) is a good starting point. When choosing a WMS, ensure it integrates seamlessly with your existing systems and any new technologies that may be added to the company’s tech stack. Additional measures to address inaccurate inventory data include using automated data collection tools like barcode scanners or RFID (Radio Frequency Identification) technology, conducting regular audits, and ensuring seamless integration with supply chain partners.